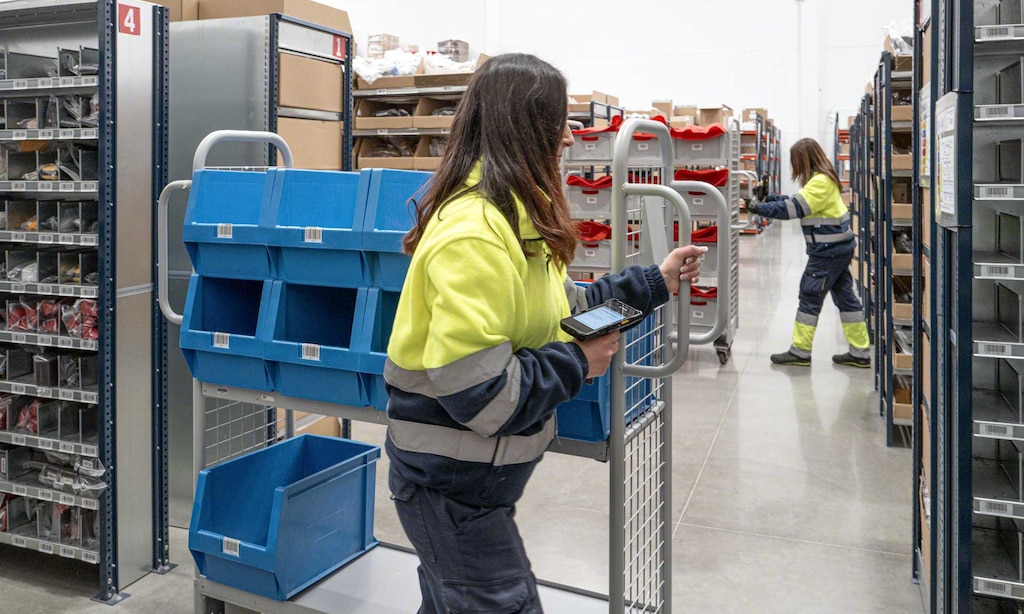
DOSSIER LOGISTIQUE
Shuya Zhong, Vaggelis Giannikas, Jorge Merino, Duncan McFarlane, Cheng Jun et Shao Wei
Le picking et le packing constituent deux processus clés dans le traitement des commandes. Le picking consiste à prélever divers articles stockés à différents endroits de l’entrepôt, tandis que le packing vise à les emballer dans différents types d’emballages tels que des boîtes, des colis ou des sacs. Ces deux opérations s’avèrent cruciales pour déterminer le temps de traitement d’une commande dans l’entrepôt, depuis le moment où elle est passée par le client jusqu’à son expédition.
La présente étude s’intéresse aux avantages de la planification intégrée du picking et du packing dans les entrepôts e-commerce. Il est primordial de considérer ces deux tâches de manière simultanée, car l’amélioration d’une seule d’entre elles n’aura qu’un impact limité en raison de leur interdépendance intrinsèque.
Néanmoins, bien qu’étroitement liés, le picking et le packing sont souvent des processus séquentiels mais indépendants, menés par deux équipes distinctes. Or, nous soutenons que la gestion intégrée du picking et du packing améliore les performances des entrepôts par rapport à l’organisation séparée de ces deux opérations.
Trois questions clés
L’objectif n’est pas uniquement d’optimiser le picking et le packing, mais également de réduire le temps d’attente entre ces deux étapes. Pour y parvenir, deux indicateurs clés ont été utilisés : le temps de traitement des commandes (le temps nécessaire pour qu’une commande soit prête à être expédiée) et la durée du cycle de production (le temps requis pas l’entrepôt pour traiter un nombre défini de commandes jusqu’à leur expédition).
Dans un entrepôt e-commerce, une commande est généralement catégorisée selon une typologie à quatre niveaux, en fonction du nombre de références et de la quantité demandée pour chacune d’entre elles : 1-référence-1-article, 1-référence-plusieurs-articles, plusieurs-références-1-article, plusieurs-références-plusieurs-articles. Cette classification a une influence directe sur les emplacements à parcourir et sur le temps de préparation et d’emballage.
L’étude tient également compte des différents niveaux de ressource en personnel affectés au picking et au packing. Afin d’évaluer les bénéfices potentiels d’une gestion intégrée, une étude expérimentale a été menée au sein d’une entreprise de stockage basée sur des données empiriques. La planification conjointe du picking et du packing a été comparée à une planification individuelle au moyen d’un modèle mathématique.
Une gestion intégrée du picking et du packing optimise les opérations en entrepôt
Ce modèle mathématique visait à répondre à trois questions : selon quels critères regrouper les commandes pour constituer une picking list optimale ? Quelle organisation adopter pour le personnel préparateur afin d’optimiser leur efficacité ? Comment et dans quel ordre attribuer les picking list aux emballeurs une fois le picking terminé pour garantir un flux fluide ?
Pour ce faire, nous avons défini les caractéristiques suivantes d’un entrepôt en nous inspirant d’études existantes sur le sujet et des opérations d’une entreprise donnée. L’installation repose sur un système de préparation de commandes à faible hauteur, où les produits sont triés en même temps qu’ils sont collectés. La zone de picking comprend plusieurs allées larges et un dépôt où chaque référence est stockée à un emplacement unique. Les préparateurs s’aident d’un chariot, toujours disponible, et effectuent des itinéraires en forme de S, tandis que les emballeurs restent à leur poste de travail.
Quatre scénarios possibles
L’entrepôt traditionnel étudié s’inscrit dans le cadre d’une plateforme logistique opérant pour le compte d’un commerçant de détail en ligne. Divers scénarios ont été analysés, impliquant des volumes de commandes variés. Chacun de ces scénarios nécessitait des quantités et des références différentes, et était réparti en un nombre variable de picking lists.
Temps d’attente et d’exécution du picking et du packing avec une méthode intégrée et une méthode non intégrée
Lorsque le nombre d'emballeurs dépasse celui des préparateurs de commandes, les économies de temps sont réalisées en amont du processus de picking
- Avec 300 commandes et un maximum de 24 picking lists, la gestion intégrée du picking et du packing a permis de réduire le temps de traitement et la durée du cycle de production. Pour y parvenir, la méthode intégrée sacrifie partiellement l’efficacité du picking pour obtenir des gains de temps significatifs dans la phase de packing.
- Dans les scénarios impliquant 100 à 600 commandes, réparties entre 8 et 48 picking lists, il apparaît qu’à mesure que le nombre de commandes augmente, les avantages d’une gestion intégrée du picking et du packing tendent à diminuer.
- L’étude de 300 commandes avec des compositions variées (avec un rapport variable entre les quatre catégories 1-référence-1-article, 1-référence-plusieurs-articles, plusieurs-références-1-article, plusieurs-références-plusieurs-articles) montre que la méthode intégrée stimule les performances. L’avantage est plus important lorsque la complexité des expéditions à préparer est modérée.
- Douze employés sont répartis de différentes manières pour faire varier le nombre de préparateurs et d’emballeurs chargés de traiter 300 commandes avec 24 picking lists. Lorsque le nombre de préparateurs est supérieur à celui des emballeurs, le principal avantage de la méthode intégrée réside dans la réduction du temps écoulé avant la phase d’emballage. En revanche, lorsqu’il y a plus d’emballeurs que de préparateurs, le gain de temps se produit avant le début du picking. Cela signifie que, dans certains scénarios où il n’est pas possible d’accélérer l’emballage, la gestion intégrée du picking et du packing n’apporte aucun avantage.
Résultats : des vagues de picking plus petites
Nos résultats révèlent que la planification intégrée du picking et du packing peut optimiser les performances dans divers contextes. Il a été démontré que se limiter uniquement sur des changements au niveau du picking ne garantit pas d’améliorations globales du système lorsque le packing demeure un goulot d’étranglement. Par ailleurs, des compromis mineurs au niveau de la gestion du picking peuvent générer des gains de temps plus importants dans la phase de packing et accroître l’efficacité globale.
De même, le nombre de commandes considéré pour la répartition du travail et les avantages que la planification intégrée peut apporter sont inversement proportionnels. Cela souligne l’importance de définir le nombre de commandes à regrouper avant de lancer tout processus, tel que le picking par vagues. Ainsi, dans la pratique, il peut être préférable d’opter pour plusieurs vagues courtes afin de maximiser les bénéfices d’une planification intégrée.
AUTEURS DE LA RECHERCHE :
- SHUYA ZHONG. Professeure associée en logistique et gestion de la chaîne d’approvisionnement à l’université de Bath (Royaume-Uni).
- VAGGELIS GIANNIKAS. Professeur en technologie et gestion des opérations et directeur du Centre for Intelligent Warehousing and Logistics Systems de l’université de Bath (Royaume-Uni).
- JORGE MERINO. Chercheur associé à l'Institute for Manufacturing de l’Université de Cambridge (Royaume-Uni).
- DUNCAN McFARLANE. Professeur d’ingénierie de l’information industrielle et chef du laboratoire d’information distribuée et d’automatisation de l’Institute for Manufacturing, département d’ingénierie, université de Cambridge (Royaume-Uni).
- JUN CHENG. Shenzhen YH Global Supply Chain Co., Ltd (Chine).
- WEI SHAO. Shenzhen YH Global Supply Chain Co., Ltd (Chine).
Publication originale :
Zhong, Shuya, Giannikas, Vaggelis, Merino, Jorge, McFarlane, Duncan, Cheng Jun, Shao Wei. 2022. « Evaluating the benefits of picking and packing planning integration in e-commerce warehouses ». European Journal of Operational Research, 301 (Elsevier).
Version disponible en libre accès ici.