
Picking par zones : la division de l’entrepôt
Comment améliorer les opérations de picking pour éviter les déplacements inutiles de l’opérateur et augmenter la productivité ? Une des solutions pour y parvenir est le picking par zones, une méthode de préparation de commandes qui consiste à diviser l’entrepôt en différentes zones, en attribuant chaque zone à un ou plusieurs opérateurs. L’objectif de cette stratégie est de réduire les distances parcourues par les travailleurs à l’intérieur de l’entrepôt pour plus d’efficacité lors de la préparation de commandes.
Dans cet article, nous vous expliquons ce qu’est le picking par zones, quels sont ses principaux avantages et inconvénients, dans quels entrepôts ou centres logistiques il peut être appliqué, et surtout, comment le mettre en pratique.
Qu’est-ce que le picking par zones ?
Le picking par zones (en anglais zone picking) consiste à diviser la zone de stockage en différents secteurs selon plusieurs critères tels que, par exemple, le type de produit, le niveau de demande, les conditions de stockage ou la quantité de références. Chaque zone se voit attribuer un certain nombre d’opérateurs responsables du picking de tout produit s’y trouvant, ce qui optimise le temps de préparation de commandes.
Le picking par zones est généralement mis en place dans des entreprises ayant de nombreuses commandes hétérogènes, comme le e-commerce, où chaque commande peut être composée d’articles de taille, d’utilisation ou de section différentes. En sectorisant le stockage, on évite les déplacements inutiles des opérateurs et des marchandises à travers l’entrepôt.
Types de picking par zones : séquentiel ou simultané ?
Pour le picking par zones, l’entrepôt est divisé en secteurs, chacun étant réservé à certain opérateurs. Lorsqu’une commande nécessite des produits provenant de plusieurs zones, cette méthode de picking peut être séquentielle ou simultanée, en fonction du nombre de commandes réalisées en même temps.
Picking par zones séquentiel (pick and pass) : Dans cette méthode, il n’y a qu’un seul bac par commande, qui traverse les différentes zones (via un convoyeur par exemple). Les opérateurs en charge de chaque zone de stockage déposent dans le bac les articles indiqués sur le bon de livraison ou le terminal radio fréquence. Lorsque le bac arrive en fin de parcours, la commande est prête.
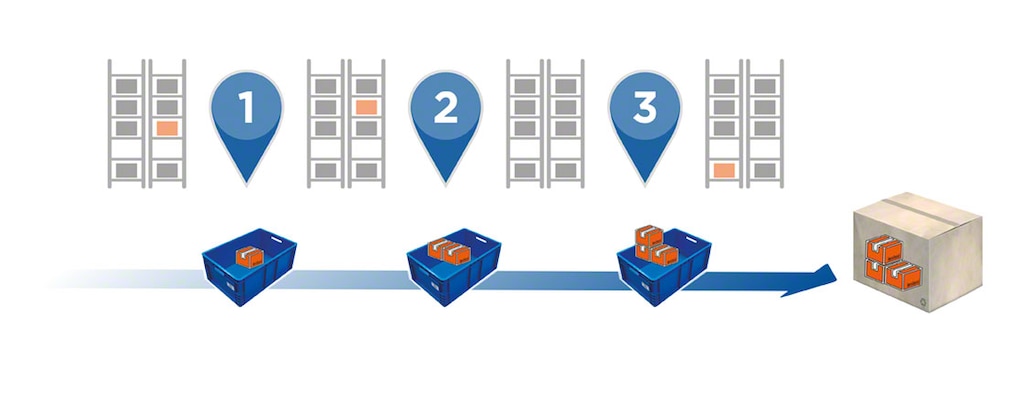
Picking par zones simultané (pick and merge) : dans ce cas, les opérateurs de chaque zone travaillent sur la même commande simultanément, chacun ayant son propre bac. De cette façon, l’opérateur d’une zone n’a pas à attendre que celui de la zone précédente ait fini pour s’occuper de la commande. Une fois que tous les opérateurs ont terminé, la commande est unifiée dans une autre zone (les produits d’une même commande sont regroupés). Sans interférence entre les opérateurs, cette stratégie permet de gagner du temps et d’accélérer le processus final de conditionnement.
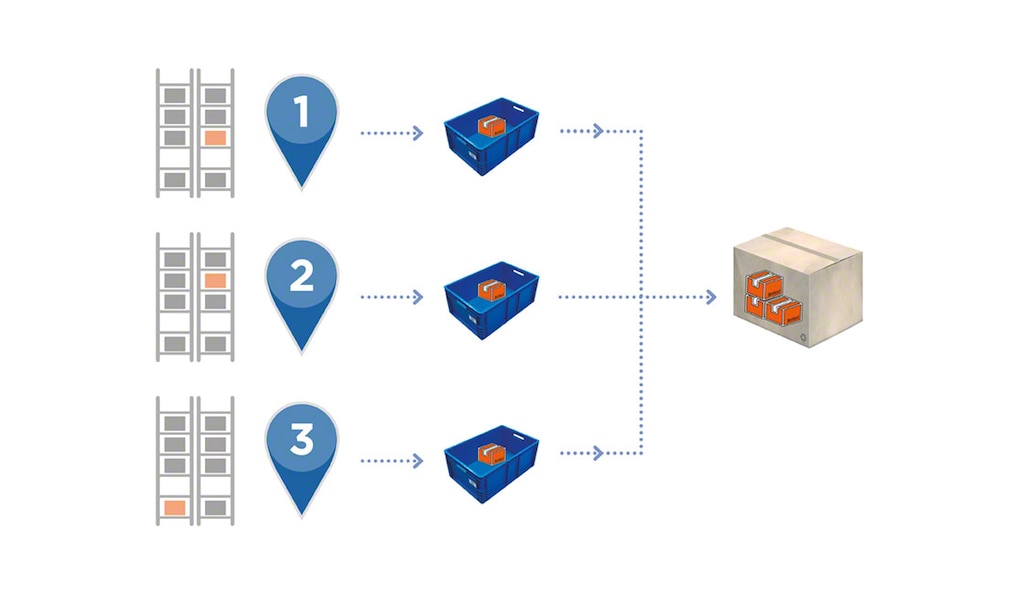
Avantages (et inconvénients) du picking par zones
Le picking par zones garantit :
- Des parcours optimisés. Il réduit les déplacements des opérateurs dans l’entrepôt, leur permettant ainsi de préparer plus de commandes en un temps imparti.
- La rapidité et la réduction des erreurs. Le système de gestion de l’entrepôt indique à l’opérateur la quantité de produit à placer dans chaque bac, ce qui accélère les opérations et limite le risque d’erreurs.
- La suppression des goulets d’étranglement. Le picking par zones fluidifie l’organisation de l’entrepôt. En limitant les trajets des opérateurs dans l’entrepôt il est possible d’éviter les goulets d’étranglement et les accidents.
- Le Slotting productif. La division de l’entrepôt en plusieurs zones garantit une gestion ordonnée des emplacements de stockage, tout en réduisant les goulets d’étranglement. Le WMS automatise la gestion des emplacements dans l’entrepôt (slotting), en s’assurant que l’emplacement et l’extraction des marchandises soient basés sur les critères prédéfinis par le responsable logistique.
- La gestion efficace d’un grand nombre de références. La sectorisation est idéale dans les entrepôts ayant un grand nombre de références, car elle limite le risque d’erreurs et les déplacements inutiles du personnel.
- La spécialisation des opérateurs. La division de l’entrepôt en zones permet aux opérateurs d’être formés aux caractéristiques et aux conditions du secteur attribué. Ils approfondissent ainsi leur connaissance du produit et sont plus productifs.
- La polyvalence. Cette méthode de préparation de commandes peut être combinée avec d’autres lorsque le responsable logistique le juge nécessaire, par exemple le batch picking, le wave picking ou des systèmes de préparation de commandes semi-automatiques.
Néanmoins, certains inconvénients sont à prendre en compte. L’application du picking par zones limite la flexibilité face à des pics de demande inattendus : la division de l’entrepôt selon des critères préétablis empêche l’affectation de plus d’opérateurs à un secteur spécifique, ce qui peut conduire à des volumes de travail inégaux.
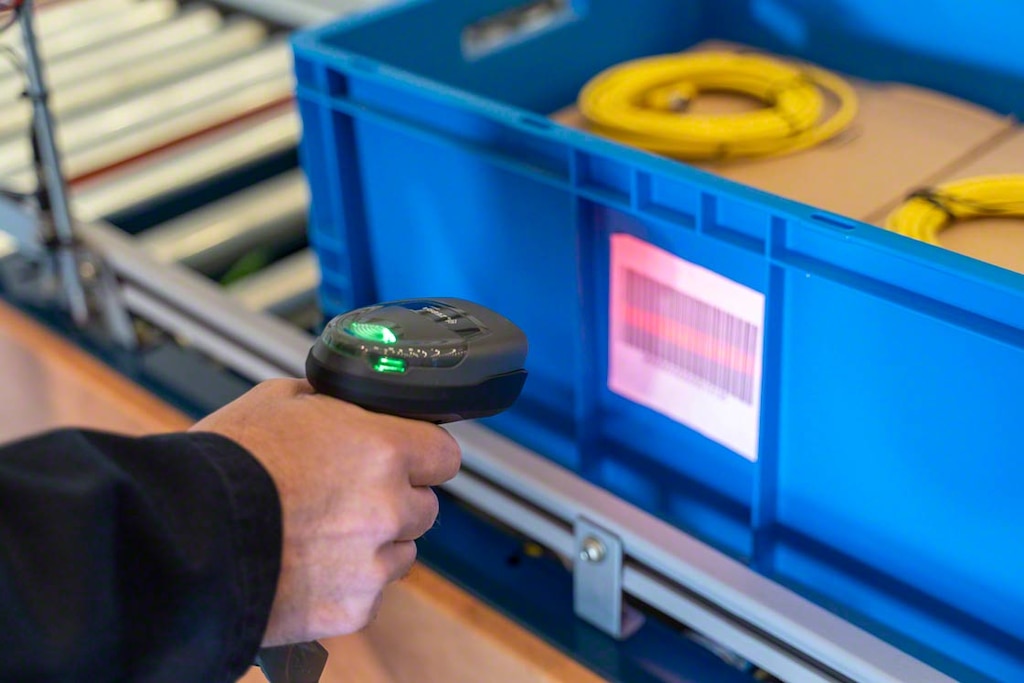
Application du picking par zones dans un entrepôt
La première étape dans la préparation de commandes par zones consiste à repenser le layout de l’entrepôt, en le divisant en différentes zones selon des critères logistiques, tels que la demande de produits, les conditions de stockage ou d’autres règles.
En outre, pour que le picking par zones soit performant il faut un logiciel de gestion d’entrepôt (WMS) qui coordonne automatiquement les déplacements des opérateurs aux flux des marchandises. Autrement dit, le système organise toutes les étapes du picking. L’opérateur, équipé de son pistolet RF, a juste à scanner l’étiquette du bac pour savoir quelles références (SKU) sont affectées à cette commande et à les placer ensuite dans le bac. En effet, le WMS remplace tout travail de gestion manuelle : il centralise toutes les commandes, gère les emplacements des articles selon des règles et des critères préétablis, organise les zones dans l’entrepôt et enfin, il indique étape par étape à l’opérateur les produits à prendre et dans quel bac les placer.
Par ailleurs, il est important que le système de gestion d’entrepôt choisi soit capable d’automatiser le slotting (gestion des emplacements) des références. De cette façon, le logiciel indique à l’opérateur dans quel emplacement chaque référence doit être placée selon des critères préalablement établis par le responsable logistique.
En complément du processus de digitalisation, il peut être judicieux de remplacer les équipements de manutention manuelle et les chariots par des systèmes automatisés tels que des convoyeurs pour bacs. Ils relient les zones de l’entrepôt pour des flux de marchandises plus rapides. En effet, l’entrepôt est généralement conçu avec des zones de stockage de produits à fort taux de rotation situées à proximité d’équipements automatisés, dans le but d’accélérer le passage des marchandises vers le poste de travail en vue de leur regroupement et de leur emballage.
Dans le cas où l’installation n’est pas automatisée, le picking par zones est réalisé à l’aide de chariots, plus ou moins grands avec des emplacements pour chaque commande, des roll containers ou des chariots préparateurs de commandes.
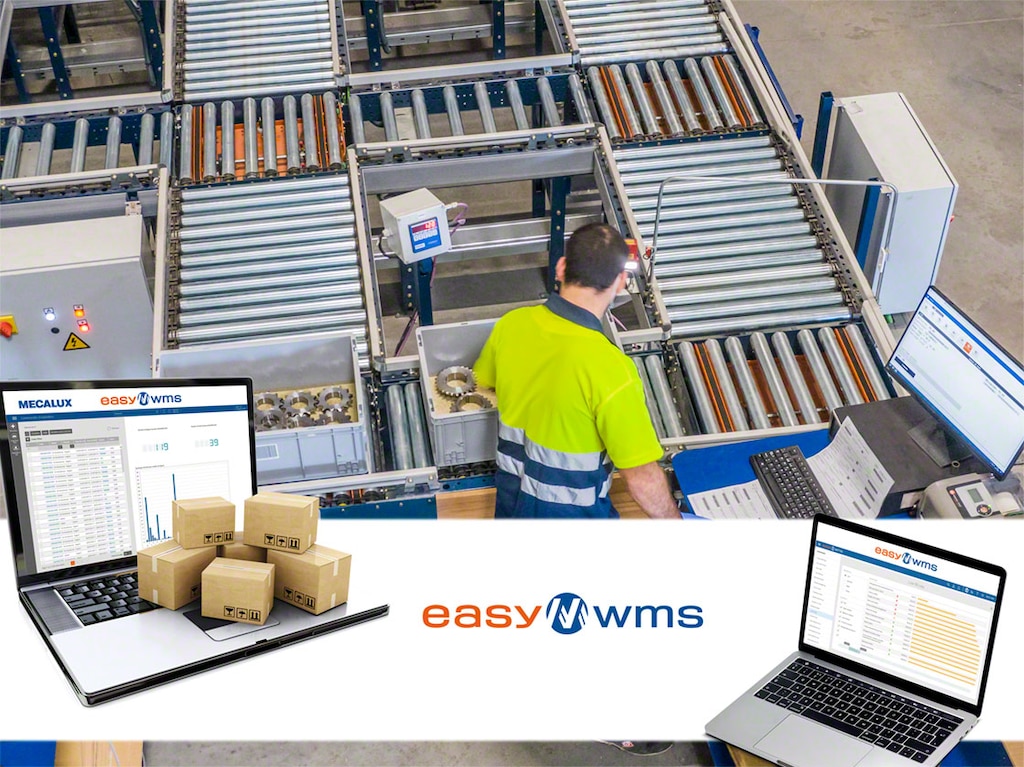
Sectorisation de l’entrepôt selon des critères logistiques
Le picking par zones est une méthode de préparation de commandes très utilisée dans les entreprises ayant beaucoup de références dans leur entrepôt, car elle permet d’éviter les mouvements inutiles en attribuant une zone à chaque opérateur. Cependant, pour son application, il est nécessaire d’installer un logiciel de gestion d’entrepôt qui coordonne les mouvements des marchandises et des opérateurs, en éliminant les erreurs dérivées de la gestion manuelle.
Si vous souhaitez plus d’efficacité dans la préparation de vos commandes, n’hésitez pas à nous contacter. Le système de gestion d’entrepôt de Mecalux, Easy WMS, est idéal pour automatiser les équipements dans votre entrepôt, depuis le picking jusqu’au slotting.