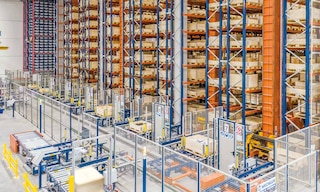
Les PLC en logistique, premier pas vers l’automatisation d’un entrepôt
La croissance des contrôleurs logiques programmables (PLC) dans le secteur de la logistique va de pair avec l’automatisation des entrepôts et des centres de production. Il s’agit de processeurs robustes dont la fonction est d’exécuter un programme d’automatisation dans des environnements logistiques et industriels.
Autrement dit, ce sont les dispositifs chargés de traiter les instructions et d’exécuter les mouvements programmés pour assurer le bon fonctionnement de l’installation automatisée.
Qu’est-ce qu’un PLC ou contrôleur logique programmable ?
Le contrôleur logique programmable (en anglais programmable logic controller) est la pierre angulaire de l’automatisation industrielle. De nombreux systèmes automatisés pour entrepôt disposent d’un processeur PLC industriel qui facilite l’automatisation des mouvements. Il est important de ne pas confondre l’acronyme PLC dans le contexte de la robotique avec la Power Line Communications, c’est-à-dire la technologie qui permet l’échange d’informations par des lignes à haute tension.
Le fonctionnement d’un PLC est le suivant : le processeur communique avec un logiciel de niveau supérieur, qui traite les informations qu’il reçoit du logiciel de gestion d’entrepôt et exécute les tâches en fonction des règles préprogrammées. Ce type de microprocesseur, généralement plus robuste qu’un PC, fonctionne en temps réel : il reçoit les informations par les canaux d’entrée et exécute les mouvements de la machine par les canaux de sortie.
Composants d’un PLC
La structure de base d’un PLC est similaire à celle d’un ordinateur, il est composé des éléments suivants :
- CPU : unité centrale de traitement qui interprète chacune des instructions programmées.
- Source d’alimentation : composant qui fournit de l’énergie électrique au CPU et aux autres éléments du PLC.
- Module de mémoire : désigne l’espace disponible du processeur où sont stockées toutes les informations nécessaires à l’exécution d’une tâche.
- Entrées et sorties : modules analogiques et numériques qui garantissent le bon fonctionnement du PLC. Les entrées traitent les informations provenant du logiciel de niveau supérieur, tandis que les sorties permettent la connexion physique entre l’ordinateur et le robot qui doit effectuer les mouvements.
- Unité de programmation : ensemble de matériel et de logiciels qui permet au PLC d’interpréter les instructions qu’il reçoit d’un autre programme dans un ou plusieurs langages de programmation.
À titre de curiosité, ces automates sont programmés à l'aide de langages tels que Ladder, très populaire dans la programmation de ce type d’appareils, basés sur des schémas de contact et de commandes standards. Ces dernières années, une norme CEI a été créée, elle régit les différents langages de programmation existants dans le but de favoriser l’utilisation d’un même programme dans les PLC de différents fabricants.
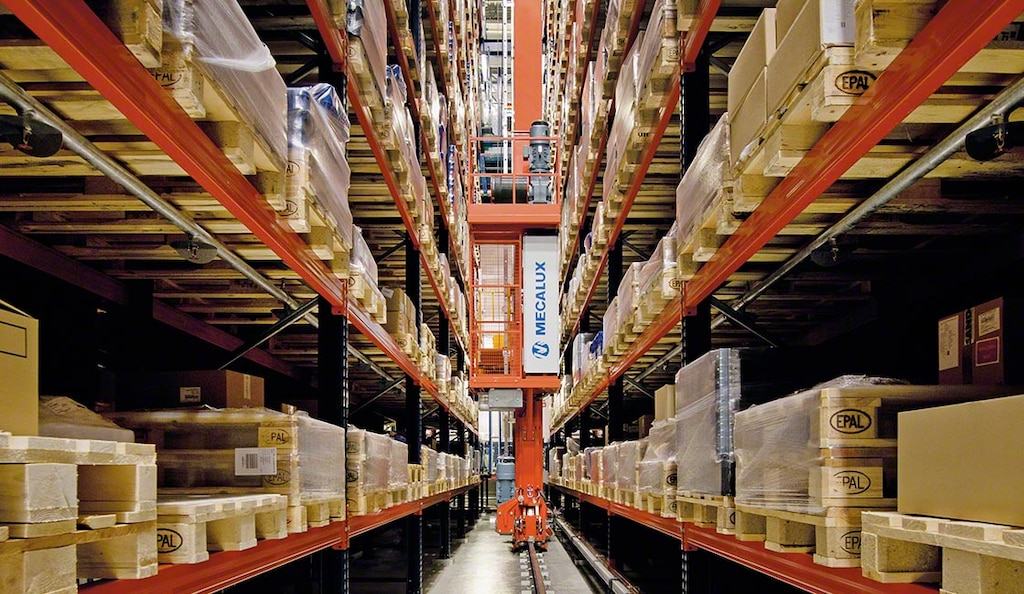
Différences entre PC et PLC
Il est commun de confondre les contrôleurs logiques programmables avec les différents PC de contrôle que l’on peut retrouver dans un entrepôt, car tous deux sont capables de piloter les mouvements d’un robot industriel sur la base d'informations reçues par un logiciel de niveau supérieur. En outre, les deux hardwares ont une structure similaire : une unité centrale, un ensemble de signaux d’entrée, de signaux de sortie et d’une mémoire.
Cependant, les automates programmables ne disposent pas de système d’exploitation, ce qui ne leur permet pas d’utiliser de bases de données. En revanche, un PC fonctionne avec un OS, c’est-à-dire un système d’exploitation, sur lequel est installé un logiciel tel que Galileo (l'automate utilisé par Mecalux dans ses installations). Il collecte des informations sur l’état de l’installation et reçoit des instructions pour déclencher le mouvement des systèmes automatisés.
Quoi qu’il en soit, un PLC présente de nombreux avantages par rapport à un PC industriel : il offre la possibilité d’intégrer des programmes de sécurité avec des entrées et des sorties plus sûres, idéales pour les processus qui ne permettent pas de marge d’erreur.
De plus, les contrôleurs logiques programmables sont un outil parfait en logistique et pour la production, car ils sont plus robustes et sont spécialement conçus avec des protections pour s’adapter à des environnements complexes (des vibrations à haute fréquence, de la corrosion ou des changements de température).
Mecalux utilise une combinaison de PC et de PLC dans ses installations, en tirant parti des avantages offerts par chacun de ces appareils.
Fonctions et applications des PLC dans les entrepôts
Les PLC constituent le premier rouage de l’automatisation des entrepôts, car ils sont aujourd’hui utilisés dans tous les systèmes robotisés. Ces processeurs robustes fonctionnent de la même manière qu’un ordinateur de bureau, à la différence qu’ils sont spécifiquement adaptés pour être utilisés dans des environnements industriels. Pourquoi ? Les systèmes d’exploitation utilisés par les ordinateurs sont moins stables que les PLC et ne sont pas spécifiquement conçus pour résister aux conditions de travail industrielles et des entrepôts.
Les PLC sont souvent installés dans des processus industriels qui nécessitent peu d’espace, le contrôle des processus ou l’utilisation de plusieurs séquences pour réaliser les différentes tâches. Leur résistance élevée en fait l’outil idéal pour exécuter les mouvements automatisés d'un entrepôt : des robots pick and place aux postes de picking dans l’industrie automobile aux systèmes de stockage automatisé dans des secteurs tels que la chimie ou pharmaceutique. En effet, une grande majorité des systèmes de stockage automatisé ou de transport automatique, tels que les miniload ou les convoyeurs pour bacs, sont contrôlés par un PLC.

La relation entre PLC, WCS et WMS
Un PLC est un matériel sur lequel est installé un programme spécialisé qui interprète les informations reçues d’un logiciel de niveau supérieur et exécute les mouvements des systèmes automatisés.
D'autre part, un WCS (warehouse control system) est un logiciel de niveau supérieur qui envoie des données au PLC ou au PC industriel afin qu’il se charge du déplacement de la machine. Ce programme informatique pilote les éléments qui contrôlent les sorties de marchandises et la gestion des emplacements. Sans entrer dans les détails, il contrôle tout, de l’itinéraire des transstockeurs pour palettes aux zones de picking, ainsi que tout élément automatisé.
Cependant, il existe encore un troisième programme logistique qui fonctionne comme le « cerveau de l’entrepôt » : il indique au WCS les instructions à envoyer aux PLC en fonction des critères d'emplacement, des stratégies de picking ou des itinéraires d’expédition paramétrables, parmi de nombreuses autres variables. Ce logiciel est le logiciel de gestion d’entrepôt (WMS).
PLC, l’un des piliers de l’automatisation industrielle
Que ce soit par le biais d’un PLC ou d’un PC équipé d’un logiciel intégré, la coordination entre les différents systèmes automatisés est essentielle pour assurer l’efficacité et la productivité d’un entrepôt. À cela, il faut ajouter que l’automatisation industrielle est de plus en plus une réalité dans les centres logistiques : d’ici 2026, le chiffre d’affaires de ce secteur devrait dépasser les 30 milliards de dollars, selon la dernière étude du cabinet de conseil LogisticsIQ.
Dans ce contexte, le bon fonctionnement de l’entrepôt automatisé nécessite des systèmes qui assurent la synchronisation entre tous les systèmes automatisés, favorisant la sécurité, la productivité et, surtout, l’efficacité de l’installation.
Mecalux dispose d’une équipe de professionnels pour la conception et la mise en œuvre d'entrepôts automatisés adaptés à votre produit, à votre installation et à vos besoins. N’hésitez pas à nous contacter, un expert vous accompagnera dans la recherche de la meilleure solution pour augmenter vos performances logistiques.